Der Entwicklungsprozess für ein kundenspezifisches Kunststoff-Extrusionsteil
Unser Entwicklungsprozess gemäß den APQP-Prinzipien
In der vom Wettbewerb bestimmten Welt der Produktion ist Qualität kein Luxus – sie ist eine absolute Notwendigkeit. Nichts kann den Ruf eines Unternehmens so schnell ruinieren wie eine mangelhafte Qualität. Die Einführung neuer Produkte – oder wesentliche Änderungen an bereits bestehenden Produkten – ist deshalb ein besonders heikler Prozess.
Das Risikomanagement und die ständige Optimierung unserer Qualitätsstandards sind wesentliche Elemente unseres Ansatzes. Das spiegelt sich in jedem Schritt unseres Entwicklungsprozesses wider. Sie interessieren sich dafür, wie wir bei Meldon kundenspezifische Kunststoff-Extrusionsteile entwickeln? In diesem Blog verraten wir Ihnen, wie wir nach den Prinzipien des APQP arbeiten.
Qualitätsmanagement-System gemäß IATF 16949
Meldon hat das Qualitätsmanagement-System gemäß IATF 16949 entwickelt. Eine der Anforderungen von IATF 16949 ist, dass wir ein sehr effektives Qualitätsmanagementsystem haben müssen. Die hohen Qualitätsstandards von IATF 16949 erfordern, dass wir bei der Einführung neuer Produkte (NPI) und bei der Serienproduktion eine Vielzahl von strengen Vorgaben einhalten. Die Einhaltung dieser Anforderungen soll Fehler und Ausfälle in den Prozessen verhindern.
Fortgeschrittene Planung der Produktqualität
Ein effektives Risikomanagement sorgt für eine bessere Kontrolle über die Qualität und einen besseren geschäftlichen Erfolg. Meldon setzt die Methode der fortgeschrittenen Produkt-Qualitätsplanung (APQP) ein. APQP minimiert die mit den Produktionsprozessen verbundenen Risiken, wie z.B. Prozessausfälle. Aus diesem Grund arbeiten wir bei neuen Produkt- und Prozessentwicklungen (NPI) nach dem APQP-Verfahren. APQP gehört zu den fünf Kern-Tools (IATF 16949-konform) für ein effektives Qualitätsmanagement, wobei PPAP, FMEA, MSA und SPC die anderen Kern-Tools sind.
APQP ist in vier Hauptphasen unterteilt:
- Planungsphase
- Phase der Produktentwicklung und Unterstützung bei der Entwicklung
- Phase der Prozessgestaltung und -entwicklung
- Phase der Produkt- und Prozessvalidierung
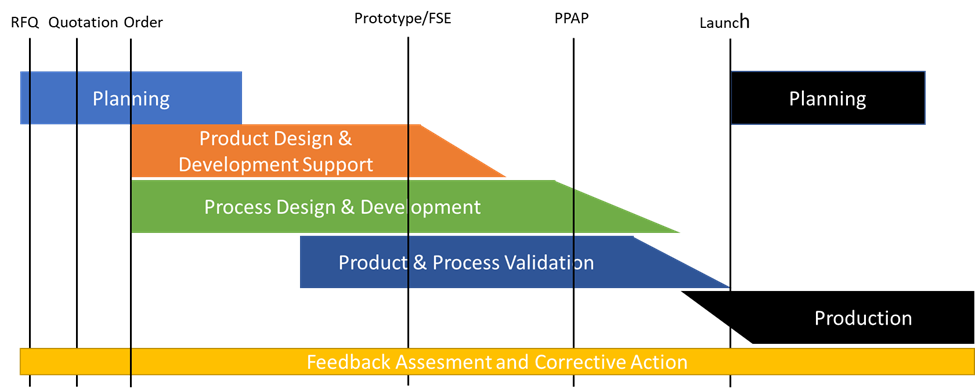
In der Regel fängt der Entwicklungsprozess für ein neues Produkt mit einer Anfrage unseres Kunden an. Dies geschieht gewöhnlich in Form einer technischen Konzeptzeichnung. Die Vertriebsabteilung bearbeitet den Antrag und beginnt den Entwicklungsprozess gemäß der APQP-Methodik. APQP bietet uns einen strukturierten Prozess, mit dem wir die Kundenzufriedenheit bei neuen Produkten sowohl in der Entwicklungsphase als auch in der Produktionsphase sicherstellen können.
Diese vier Phasen möchten wir anhand unseres internen Prozesses zur Entwicklung eines neuen Extrusionsprofils näher beschreiben.
1. Planungsphase: Sammeln von Informationen
Eine der wichtigsten Informationen in der Planungsphase ist die erwartete Funktion der extrudierten Teile beziehungsweise der Baugruppe. Diese Informationen helfen dem Konstruktionsteam dabei, im Rahmen einer Machbarkeitsstudie die Anfrage und die potenziellen Einschränkungen bei der Konstruktion zu beurteilen. Bei einfachen Produkten ist der Prozess recht unkompliziert. Wenn es sich jedoch um einen komplexen Entwurf handelt, wird ein Treffen mit allen beteiligten Parteien organisiert. Während dieses Treffens besprechen wir alle Details, darunter:
- die Verwendung
- den Verwendungszweck des Profils
- die betreffenden Toleranzen
- das angegebene Material
- die eventuell zu überwindenden Hindernisse
- die Betriebsumgebung des Teils
- etwaige (spezifische) Kundenwünsche
Wir lassen uns in unserer Bewertungs- und Planungsphase von all diesen Informationen leiten.
Nach diesem Informationsaustausch beginnen wir mit dem Entwurf eines extrudierten Profils, bei dem alle Elemente berücksichtigt werden. Eines unserer Ziele ist es, ein Teil zu entwerfen, das der Anwendung entspricht, die der Kunde im Sinn hat. Dazu gehört eine Analyse der erforderlichen Toleranzen und der Passform. Ein zweites Ziel ist es, ein Profil zu entwerfen, das für den Extrusionsprozess optimiert ist. Das ist wichtig, weil das Endziel darin besteht, ein Profil zu definieren, das sowohl kosteneffizient als auch gleichbleibend zuverlässig ist.
Technische Zeichnungen und Kostenvoranschlag
Gegebenenfalls reichen wir dann eine technische Zeichnung ein oder machen Änderungsvorschläge zu den vom Kunden gelieferten Zeichnungen. Dank unserer langjährigen Erfahrung mit dem Extrudieren wissen wir, dass bestimmte Profile eine Herausforderung für den Extrusionsvorgang darstellen können. Bei der Gestaltung des Profils berücksichtigen wir natürlich so viele Faktoren wie möglich. Es ist allerdings wichtig, dass Sie uns mitteilen, welche Ergebnisse Sie erwarten, um sicherzustellen, dass wir Ihre Erwartungen auch erfüllen. Sobald wir uns über das vorgeschlagene Design (und gegebenenfalls Änderungen) geeinigt haben, werden wir Ihnen ein schriftliches Angebot machen.
2. Phase der Produktentwicklung und Unterstützung bei der Entwicklung
Sobald wir den Auftrag erhalten haben, mit der Entwicklung des Profils fortzufahren, wird die zweite Phase des APQP-Prozesses in Angriff genommen: „Produktdesign und Unterstützung bei der Entwicklung“. Wir suchen Lieferanten aus und fangen an, die Werkzeuge und Messelemente zu entwerfen, die für die Herstellung des Profils erforderlich sind. Das Ziel dieser Phase ist die Vollendung des Produktdesigns und die Beurteilung der Machbarkeit.
3. Phase der Prozessgestaltung und -entwicklung
In Phase 3 „Prozessgestaltung und -entwicklung“ planen wir den Herstellungsprozess für das Produkt. Bei der Konzeption und Entwicklung des Produktionsprozesses müssen die Produktspezifikationen, die Qualität des Produkts und die Produktionskosten berücksichtigt werden. Der Prozess muss reibungslos ablaufen und die gewünschten Mengen produzieren können, um mit der Nachfrage seitens der Käufer Schritt zu halten.
Erste Auswertungen und Testläufe
In dieser Phase wird von einem multidisziplinären Team eine Prozess-FMEA vorgenommen.
Aus der p-FMEA wird dann ein Kontrollplan erstellt. Die Werkzeuge werden in unserem eigenen Werkzeugbau hergestellt. Wenn alle Elemente fertiggestellt sind, werden die Werkzeuge für den ersten Probelauf auf einen Extruder montiert, um den Fluss des/der Kunststoffs/Kunststoffe zu beurteilen.
Bei komplexen Profilen verfolgt jeder Test sein eigenes Ziel, je nachdem, welches Element der Form wir zu dem jeweiligen Zeitpunkt zu bewerten versuchen. Nach jedem Test werden Änderungen an den Werkzeugen vorgenommen, die uns dem fertigen Teil näherbringen. Ein typisches Profil bedarf einer Reihe von Versuchen, bevor die Muster für die Beurteilung durch den Kunden zur Verfügung stehen.
Beurteilung der ersten Probe
Wenn die Form fertiggestellt ist, werden sogenannte First Sample Evaluation (FSE) Muster zur Beurteilung des Designs an den Kunden geschickt. Ab diesem Zeitpunkt sind wir in der Lage, den Bedarf des Kunden an zusätzlichen Mustern oder der Produktion zu decken. Sobald eine Extrusion abgeschlossen ist, das Verfahren zuverlässig läuft und das Produkt den (Kunden-)Anforderungen gerecht wird, kann mit Phase 4 begonnen werden.
4. Phase der Produkt- und Prozessvalidierung
Hierbei handelt es sich um die Phase, in der das Herstellungsverfahren und das Endprodukt in einer Produktionsumgebung mit Mitarbeitern getestet werden. Zu den Ergebnissen dieser Phase gehört die Bestätigung, dass der Fertigungsprozess funktioniert und zuverlässig ist, sowie die Akzeptanzkriterien hinsichtlich der Produktqualität. Es werden Probeläufe (PPAP) durchgeführt und die Produktausgabe wird getestet, um die Effektivität des implementierten Fertigungsverfahrens zu bestätigen. Eventuell notwendige Anpassungen werden vor dem Übergang zur eigentlichen Produktion vorgenommen.
Produktion und Optimierung
In dieser Phase findet die Produktion statt, wobei der Schwerpunkt auf der Beurteilung und Verbesserung der Prozesse liegt. Aktivitäten wie die Minimierung von Prozessabweichungen, die Identifizierung von Problemen und die Umsetzung von Abhilfemaßnahmen zur Unterstützung der kontinuierlichen Verbesserung sind die wichtigsten Elemente in dieser Phase. Das Einholen und Bewerten von Kundenrückmeldungen sowie das Erfassen von Daten zur Prozesseffizienz und zur Effektivität der Qualitätsplanung sind wichtige Aspekte dieser Phase.
Wie können wir Ihnen helfen?
Bitte zögern Sie nicht, sich für weitere Informationen oder eine Anfrage an uns zu wenden.